Product line → Infotech.Resultat
Integrated automation system
for energy providers
Increase the operational
efficiency of facilities
Monitor and predict
infrastructure status online
Ready-made IT solutions for power grid companies
Order integrated implementation
or purchase systems separately
Task Management
More
Minimize
CMMS Management
More
Minimize
Outdoor lighting control
More
Minimize
Accident and Failure Forecasting
More
Minimize
Task management system and planning the work of field service teams
The system makes it possible to promptly receive and process users’ requests, dispatching requests and information from mobile inspectors about technological disruptions in the operation of distribution networks and outdoor lighting systems. The creation of job cards for field service teams by supervisors and control over the execution of works are automated.
The system can be integrated
with city portals
Supported platforms:
iOS
Android
System supervisor’s web interface
Mobile application for field service teams
Features for system users
System supervisor:
- Centralized reception and processing of applications coming from various sources: city portal, dispatching systems, street lighting control systems, etc.
- Automated creation and assignment of job cards to inspectors
- Tasks assignment based on current information on location and workload of field teams
- Monitoring compliance with the scheduled troubleshooting deadlines
- Monitoring the quantity and quality of work
- Automated reporting
- Collection of statistics on works performed, and on the replacement and repair of equipment
Field service teams:
- Access to tasks for inspection, diagnosis and repair
- Detailed information (data, maps, diagrams) about the equipment to be repaired and its location
- Identification of equipment using the QR code, barcode and augmented reality technology
- GPS positioning
- Online transfer of equipment status data and work results to the system
Features of
the system
Minimize
Equipment Maintenance and Repair Management System
The system stores accurate and complete information about the equipment’s technical data sheets, the history of its inspections, diagnostics and repairs, providing information support for decision-making. Requests for scheduled and urgent repairs are registered, submitted, considered and coordinated automatically.
The solution is integrated with the electronic document management system, and Supervisory Control And Data Acquisition (SCADA)
Supported platforms:
iOS
Android
System supervisor web interface for the approval of repair requests
Field service teams’ mobile application of field teams for data entry and information retrieval
Features for system users
System supervisor:
- Monitoring the execution of requested tasks
Maintenance service:
- Full and up-to-date information for maintenance management and repair planning
- Coordination of repair schedules and requests with other divisions and related enterprises
- Cost planning for maintenance and replacement of power equipment
- Automatic reporting
Field service teams:
- Access to tasks for inspection, diagnosis and repair
- Get detailed information (data, maps, diagrams) about necessary equipment and its location
- Identification of equipment using QR code, barcode and augmented reality technology
- GPS positioning
- Online transfer of facility status data and work results to the system
Features of
the system
Minimize
Outdoor lighting control system
The system automates the identification of faulty external lighting equipment. The inspectors can promptly transmit accurate data on the detected problems in the network operation and non-operational status of the facilities, to the system sypervisor.
The product is integrated
with the accounting system
Supported platforms:
iOS
Android
The geoportal displaying external lighting equipment, inspection routes and current location of inspectors
The geoportal displaying external lighting equipment, inspection routes and current location of inspectors
Web interface of the system supervisor for viewing detailed information about problems identified, creating job assignments and generating reports
Inspectors’ mobile application for on-site inspections
Features for system users
System Supervisor:
- Up-to-date online information from field inspectors for timely assignment of requests for repair works
- Automatic collection of statistics on problems detected for repair planning
- Automated reporting
Field Inspector:
- Prompt transmission of information about problems detected to the system
- Option to obtain detailed information needed for operational repair (creating a geo-tag, indicating the type of failure, the brand of defective equipment, location of the power point, a picture of defective equipment)
- Timely updating of information on street lighting equipment in the system
- Entering new facilities into the system
Features of
the system
Minimize
System for smart monitoring and forecasting of status and failures of substation power equipment
The system detects regularities in the functioning of primary and secondary substation equipment: power transformers, switching equipment, cable lines, relay protection and automation systems, telecommunications, etc. Based on this data, the system builds forecast models, determines the probability of accidents and makes recommendations for repairs and replacement of technical equipment.
The solution is integrated with existing systems for dispatching control and equipment monitoring
Supported platforms:
iOS
Android
System supervisor’s web interface
Features of the system
- Identification of patterns in the modes of operation of primary equipment, shutdowns for protection and emergencies, and failures
- Visualization of data from monitoring systems in a single window
- Dynamic determination of power line transmission capacity
- Forecasting the failure of substation power equipment
Features of
the system
Minimize
Task Management
More
Minimize
CMMS Management
More
Minimize
Task management system and planning the work of field service teams
The system makes it possible to promptly receive and process users’ requests, dispatching requests and information from mobile inspectors about technological disruptions in the operation of distribution networks and outdoor lighting systems. The creation of job cards for field service teams by supervisors and control over the execution of works are automated.
The system can be integrated
with city portals
Supported platforms:
iOS
Android
System supervisor’s web interface
Mobile application for field service teams
Features for system users
System supervisor:
- Centralized reception and processing of applications coming from various sources: city portal, dispatching systems, street lighting control systems, etc.
- Automated creation and assignment of job cards to inspectors
- Tasks assignment based on current information on location and workload of field teams
- Monitoring compliance with the scheduled troubleshooting deadlines
- Monitoring the quantity and quality of work
- Automated reporting
- Collection of statistics on works performed, and on the replacement and repair of equipment
Field service teams:
- Access to tasks for inspection, diagnosis and repair
- Detailed information (data, maps, diagrams) about the equipment to be repaired and its location
- Identification of equipment using the QR code, barcode and augmented reality technology
- GPS positioning
- Online transfer of equipment status data and work results to the system
Features of
the system
Minimize
Equipment Maintenance and Repair Management System
The system stores accurate and complete information about the equipment’s technical data sheets, the history of its inspections, diagnostics and repairs, providing information support for decision-making. Requests for scheduled and urgent repairs are registered, submitted, considered and coordinated automatically.
The solution is integrated with the electronic document management system, and Supervisory Control And Data Acquisition (SCADA)
Supported platforms:
iOS
Android
System supervisor web interface for the approval of repair requests
Field service teams’ mobile application of field teams for data entry and information retrieval
Features for system users
System supervisor:
- Monitoring the execution of requested tasks
Maintenance service:
- Full and up-to-date information for maintenance management and repair planning
- Coordination of repair schedules and requests with other divisions and related enterprises
- Cost planning for maintenance and replacement of power equipment
- Automatic reporting
Field service teams:
- Access to tasks for inspection, diagnosis and repair
- Get detailed information (data, maps, diagrams) about necessary equipment and its location
- Identification of equipment using QR code, barcode and augmented reality technology
- GPS positioning
- Online transfer of facility status data and work results to the system
Features of
the system
Minimize
Outdoor lighting control
More
Minimize
Accident and Failure Forecasting
More
Minimize
Outdoor lighting control system
The system automates the identification of faulty external lighting equipment. The inspectors can promptly transmit accurate data on the detected problems in the network operation and non-operational status of the facilities, to the system sypervisor.
The product is integrated
with the accounting system
Supported platforms:
iOS
Android
The geoportal displaying external lighting equipment, inspection routes and current location of inspectors
The geoportal displaying external lighting equipment, inspection routes and current location of inspectors
Web interface of the system supervisor for viewing detailed information about problems identified, creating job assignments and generating reports
Inspectors’ mobile application for on-site inspections
Features for system users
System Supervisor:
- Up-to-date online information from field inspectors for timely assignment of requests for repair works
- Automatic collection of statistics on problems detected for repair planning
- Automated reporting
Field Inspector:
- Prompt transmission of information about problems detected to the system
- Option to obtain detailed information needed for operational repair (creating a geo-tag, indicating the type of failure, the brand of defective equipment, location of the power point, a picture of defective equipment)
- Timely updating of information on street lighting equipment in the system
- Entering new facilities into the system
Features of
the system
Minimize
System for smart monitoring and forecasting of status and failures of substation power equipment
The system detects regularities in the functioning of primary and secondary substation equipment: power transformers, switching equipment, cable lines, relay protection and automation systems, telecommunications, etc. Based on this data, the system builds forecast models, determines the probability of accidents and makes recommendations for repairs and replacement of technical equipment.
The solution is integrated with existing systems for dispatching control and equipment monitoring
Supported platforms:
iOS
Android
System supervisor’s web interface
Features of the system
- Identification of patterns in the modes of operation of primary equipment, shutdowns for protection and emergencies, and failures
- Visualization of data from monitoring systems in a single window
- Dynamic determination of power line transmission capacity
- Forecasting the failure of substation power equipment
Features of
the system
Minimize
Task Management
More
Minimize
Task management system and planning the work of field service teams
The system makes it possible to promptly receive and process users’ requests, dispatching requests and information from mobile inspectors about technological disruptions in the operation of distribution networks and outdoor lighting systems. The creation of job cards for field service teams by supervisors and control over the execution of works are automated.
The system can be integrated
with city portals
Supported platforms:
iOS
Android
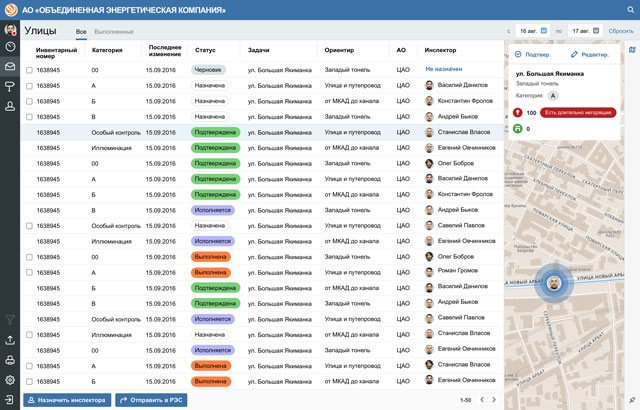
System supervisor’s web interface
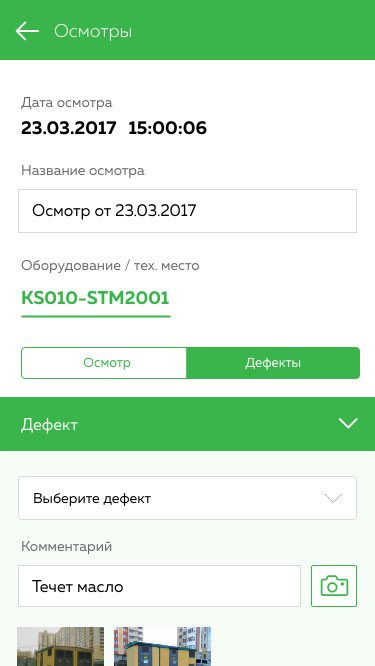
Mobile application for field service teams
Features for system users
System supervisor:
- Centralized reception and processing of applications coming from various sources: city portal, dispatching systems, street lighting control systems, etc.
- Automated creation and assignment of job cards to inspectors
- Tasks assignment based on current information on location and workload of field teams
- Monitoring compliance with the scheduled troubleshooting deadlines
- Monitoring the quantity and quality of work
- Automated reporting
- Collection of statistics on works performed, and on the replacement and repair of equipment
Field service teams:
- Access to tasks for inspection, diagnosis and repair
- Detailed information (data, maps, diagrams) about the equipment to be repaired and its location
- Identification of equipment using the QR code, barcode and augmented reality technology
- GPS positioning
- Online transfer of equipment status data and work results to the system
Features of
the system
Minimize
CMMS Management
More
Minimize
Equipment Maintenance and Repair Management System
The system stores accurate and complete information about the equipment’s technical data sheets, the history of its inspections, diagnostics and repairs, providing information support for decision-making. Requests for scheduled and urgent repairs are registered, submitted, considered and coordinated automatically.
The solution is integrated with the electronic document management system, and Supervisory Control And Data Acquisition (SCADA)
Supported platforms:
iOS
Android
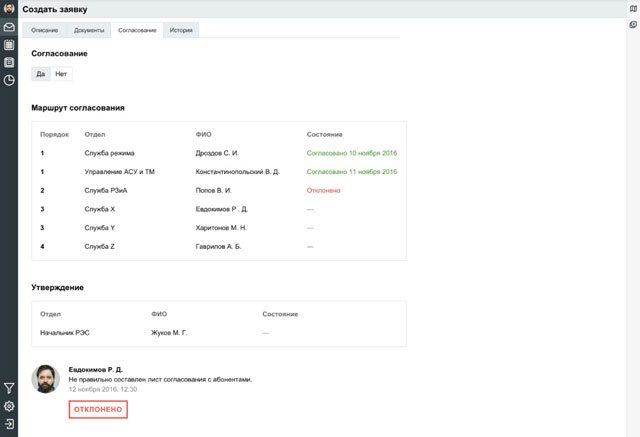
System supervisor web interface for the approval of repair requests
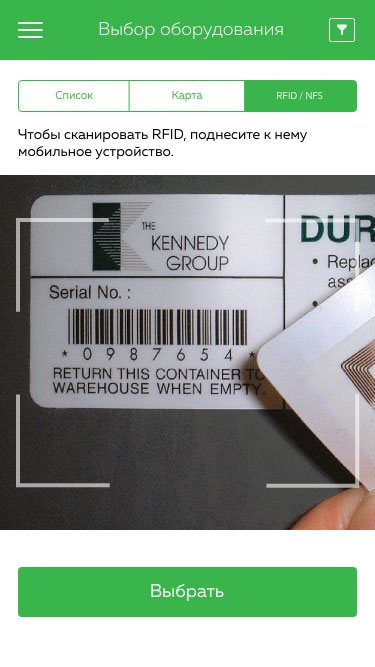
Field service teams’ mobile application of field teams for data entry and information retrieval
Features for system users
System supervisor:
- Monitoring the execution of requested tasks
Maintenance service:
- Full and up-to-date information for maintenance management and repair planning
- Coordination of repair schedules and requests with other divisions and related enterprises
- Cost planning for maintenance and replacement of power equipment
- Automatic reporting
Field service teams:
- Access to tasks for inspection, diagnosis and repair
- Get detailed information (data, maps, diagrams) about necessary equipment and its location
- Identification of equipment using QR code, barcode and augmented reality technology
- GPS positioning
- Online transfer of facility status data and work results to the system
Features of
the system
Minimize
Outdoor lighting control
More
Minimize
Outdoor lighting control system
The system automates the identification of faulty external lighting equipment. The inspectors can promptly transmit accurate data on the detected problems in the network operation and non-operational status of the facilities, to the system sypervisor.
The product is integrated
with the accounting system
Supported platforms:
iOS
Android
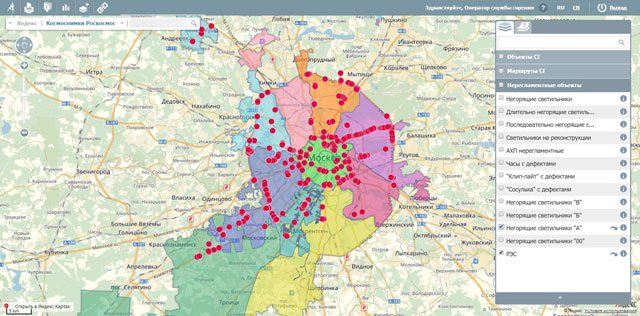
The geoportal displaying external lighting equipment, inspection routes and current location of inspectors
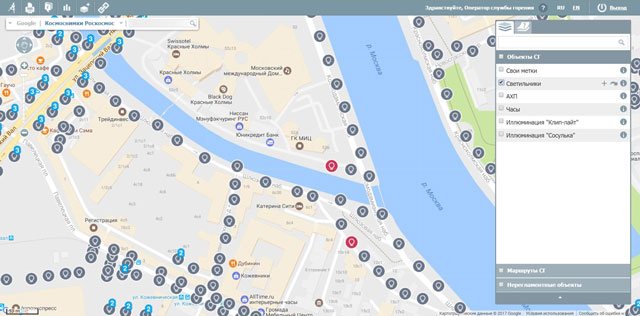
The geoportal displaying external lighting equipment, inspection routes and current location of inspectors
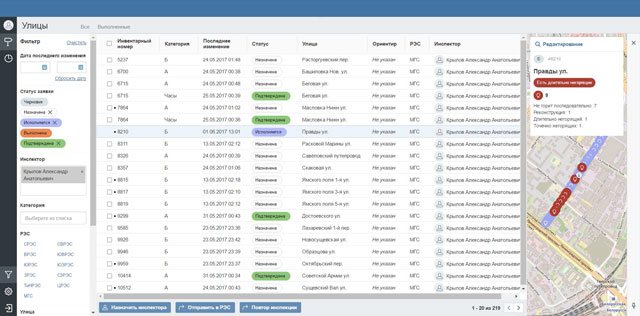
Web interface of the system supervisor for viewing detailed information about problems identified, creating job assignments and generating reports
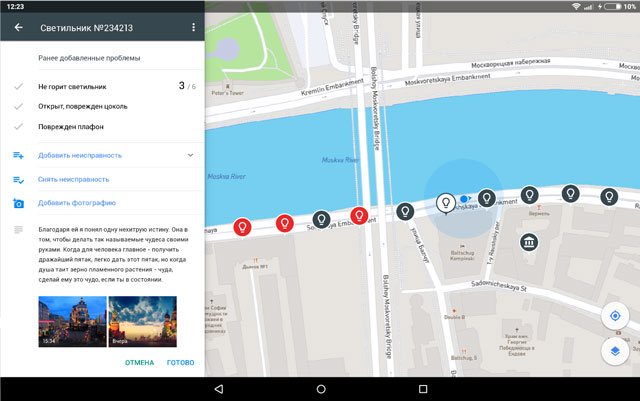
Inspectors’ mobile application for on-site inspections
Features for system users
System Supervisor:
- Up-to-date online information from field inspectors for timely assignment of requests for repair works
- Automatic collection of statistics on problems detected for repair planning
- Automated reporting
Field Inspector:
- Prompt transmission of information about problems detected to the system
- Option to obtain detailed information needed for operational repair (creating a geo-tag, indicating the type of failure, the brand of defective equipment, location of the power point, a picture of defective equipment)
- Timely updating of information on street lighting equipment in the system
- Entering new facilities into the system
Features of
the system
Minimize
Accident and Failure Forecasting
More
Minimize
System for smart monitoring and forecasting of status and failures of substation power equipment
The system detects regularities in the functioning of primary and secondary substation equipment: power transformers, switching equipment, cable lines, relay protection and automation systems, telecommunications, etc. Based on this data, the system builds forecast models, determines the probability of accidents and makes recommendations for repairs and replacement of technical equipment.
The solution is integrated with existing systems for dispatching control and equipment monitoring
Supported platforms:
iOS
Android
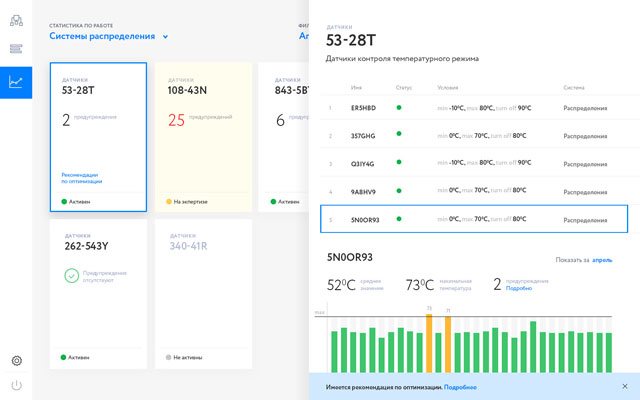
System supervisor’s web interface
Features of the system
- Identification of patterns in the modes of operation of primary equipment, shutdowns for protection and emergencies, and failures
- Visualization of data from monitoring systems in a single window
- Dynamic determination of power line transmission capacity
- Forecasting the failure of substation power equipment
Features of
the system
Minimize
Would you like to know the cost of implementation?
Implementation results
-
Complex monitoring of the condition and operation of infrastructure
-
Reduction of equipment maintenance costs
-
Automation of compliance monitoring
-
Better coordination and efficiency of the activities of workers and divisions
-
Automated task monitoring
-
Integrated analytics for work planning and failure prediction
Completed projects

INFOTECH.RESULTAT monitors outdoor lighting
on the streets of Moscow
Problem
Solution
Results
Prior to the introduction of the system, the Unit recorded the failures identified during field inspections on paper logs, they marked the faulty equipment on the map manually, then they transferred the data to an Excel table after the inspection was completed, and only afterwards passed the information to the system supervisors. The manual data transfer took almost 2 hours of an inspector’s working shift. This time could have been used to assess the condition of outdoor lighting equipment.
Thus, inspectors spent a lot of time on paperwork, and information about technical failures was transferred to the operation service with a considerable delay. However, the positioning of faulty equipment was not very accurate. The job cards were also assigned to inspectors manually, on paper, and it took much effort to control the frequency of their issue.
More than
500,000
streetlights
Creating a system for monitoring the condition of outdoor lighting, including the lighting of architectural monuments and objects of art.
- A geoportal displaying the location of all the equipment and detailed information about it
- System Supervisor’s interface for operational task management
- Mobile application with an interactive map of equipment for inspectors
-
The inspectors now spend more time in the field and have the time to inspect significantly more equipment
-
Data about equipment failures are recorded in the system and instantly transmitted to system supervisors
-
A unified register of identified failures is maintained
-
Due to the automation of the process, repair requests are processed and transferred to the operational unit without delay
-
An accurate map of the zones of operational responsibility of the units is created, with detailed information on all the monitored outdoor lighting equipment
Problem
Prior to the introduction of the system, the Unit recorded the failures identified during field inspections on paper logs, they marked the faulty equipment on the map manually, then they transferred the data to an Excel table after the inspection was completed, and only afterwards passed the information to the system supervisors. The manual data transfer took almost 2 hours of an inspector’s working shift. This time could have been used to assess the condition of outdoor lighting equipment.
Thus, inspectors spent a lot of time on paperwork, and information about technical failures was transferred to the operation service with a considerable delay. However, the positioning of faulty equipment was not very accurate. The job cards were also assigned to inspectors manually, on paper, and it took much effort to control the frequency of their issue.
More than
500,000
streetlights
Solution
Creating a system for monitoring the condition of outdoor lighting, including the lighting of architectural monuments and objects of art.
- A geoportal displaying the location of all the equipment and detailed information about it
- System Supervisor’s interface for operational task management
- Mobile application with an interactive map of equipment for inspectors
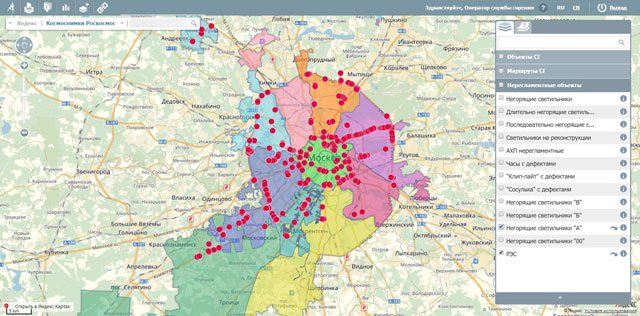
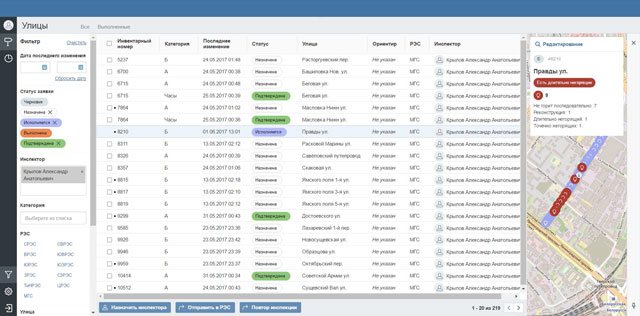
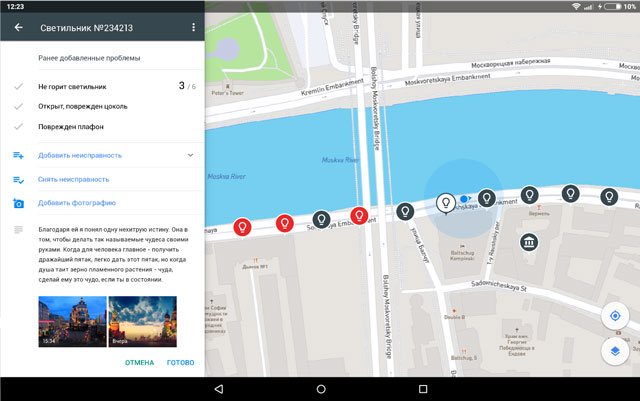
Results
-
The inspectors now spend more time in the field and have the time to inspect significantly more equipment
-
Data about equipment failures are recorded in the system and instantly transmitted to system supervisors
-
A unified register of identified failures is maintained
-
Due to the automation of the process, repair requests are processed and transferred to the operational unit without delay
-
An accurate map of the zones of operational responsibility of the units is created, with detailed information on all the monitored outdoor lighting equipment
Vladimir I. Azarnov
Head of the Unit for Monitoring the Condition
of Outdoor Lighting Facilities
"The system developed by the Infotech Group significantly optimized the work of the employees of the Unit for Monitoring the Condition of Outdoor Lighting, and the relations of the Unit with other departments of the JSC United Energy Company. The automation of key business processes has increased the productivity of inspectors’ work by 30%”.
Do you still have questions about the product?
Send a request: our business analyst will contact you
with more detailed information.